ACIDIC / SILICA RAMMING MASS
Karnataka Silicates are the manufacturer of Ramming Mass to give material as per the furnace capacity and make of the user. The Ramming Mass of the mix is optimized keeping in view the furnace make and capacity, thus giving maximum and best results. Ramming mix is characterized by thermal stability, corrosion resistance and wears resistance because it contains fewer binders, fire clay, and moisture compared to plastic refractories. Recommended for lining the iron melting coreless induction furnace. Premixed with a binder to customer's specifications. Maximum recommended use limit-3274°F(1700°C). Various grades of Ramming Mass keeping in view the different needs, different types of scraps, end products, and several other factors.
Acidic Ramming Mass is used in the lining of induction furnaces. Quality of Acidic Ramming mass is directly related to the heating performance of the furnaces. Better quality of lining results in the smooth working of furnaces, optimum output and better metallurgical control. It is manufactured under strict supervision of qualified & experienced work force. Proper check is exercised on magnetic process to assure iron free material and to assure proper composition of granules according to furnace capacity.The granulation of the mix are optimized keeping in view the furnace make and capacity, thus giving maximum and best results. It is characterized by thermal stability, corrosion resistance and wear resistance because it contains less binders, fire clay and moisture compared to plastic refractories.
The lining is the important part of induction furnace, Furnace performance is directly related to the Lining performance. Well – stabilized lining results In the smooth working of the furnace, optimum output, and Better metallurgical control. The lining practice best Suited to particular foundry will depend upon the furnace Capacity and design, metal being melted and output etc.
we offer the best quality Grades of Premixed Ramming Mass to our customers. These products are produced using high-grade inputs that are sourced from authorized merchants of the business, we offer these products according to the specifications of the customers. Moreover, these products are available at industry competitive costs. At the same time we make sure that these products are delivered within a given time period.
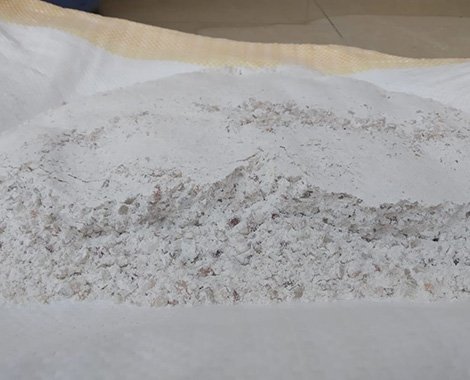
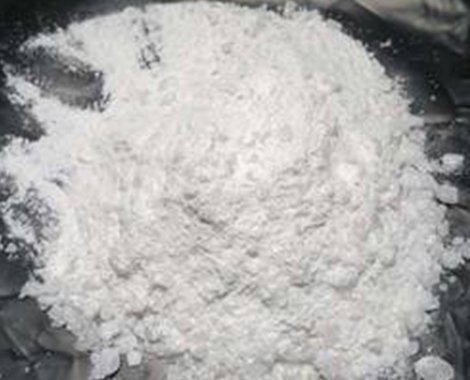
Product Specification
- Proper mixing of binder leading to optimum mixture.
- Less wastage, as mixing is done by machines.
- Imported Boric Acid is used to give best results.
- Consistent and longer lining and patching life.
- One less item in inventory.
Brand |
Phenolite and Himanshi® |
Application Area |
induction furnace |
Grain Size |
0-6 mm |
Temperature |
1730 |
Type |
Refractory |
Service Temp |
1730 |
Usage/Application |
steel industry |
Color |
White |
Sio2 |
98.5-99.5 % |
We have got different grades
- Himanshi : This is the widely used grade of Silica Ramming Mix. Silica content here is in the range of 97.50 % to 99 %. performance is the best in
- Phenolite : This is the pre-mixed version. We mix Boric Acid as per customer requirements, although most common in India is 1.2 %.
- KS Special : This is the pre-mixed version. We mix Boron Acid as per customer requirements, although most common in India is 0.5 %.
Features
Used In
- Metallurgy
- Furnaces